(Simio社製”Simio”)
従来のスケジューリングシステムの問題点
スケジューリングは、多くの産業分野において必要とされる重要な業務ですが、コンピュータを使ってシステム化を行う上では、依然として課題を残すことが多い業務でもあります。スケジューリング作業が極めて容易でホワイトボードに書けば済むような場合は別として、ある程度の複雑さを伴うスケジューリング作業を対象とした場合の従来からのシステム化のアプローチは、大別すると下記の表に示すように3種類に分類できると考えられます。
表-1. スケジューリング業務に対する代表的な3つのアプローチ
アプローチ | 内容 | 問題点 |
① 人とエクセルシート
|
必要なリソースや守るべき制約条件をエクセルシート上でチェックしながら、基本的には人がトライアル&エラーでスケジュールを作成する
|
|
② 制約条件付き最適化
|
目的関数と制約条件を数式で表して、数理計画法もしくはその他のアルゴリズムにより、実行可能解の内より良い目的関数を持つ解を探索する
|
|
③ シミュレーションと経験則
|
(簡易な)シミュレーションモデルを使って、モデルの要求する制約条件を満足しつつ、あらかじめ定めれた経験則に基づきリソースに作業時間を逐次割り当てていく |
|
①の方法は、スケジューリングの対象がある程度の複雑さとボリュームを超えない範囲では、一番よく利用される方法かもしれません。その大きな理由は、上記の表に示したような種々の問題点はあるものの、コンピュータ上ではモデル化の難しい様々な因子を考慮できる柔軟性にあるように思われます。たとえば、経験に基づいて将来の変動要因とその影響を推定しあらかじめスケジュールに反映しておくとか、その時の状況に応じてスケジュールの優先度を変えるとか、与条件として与えらる数値の信頼性や重要度を推し量るといったことは、コンピュータよりも人の方が得意です。
②の方法は、数式で表すモデルと現実がよく一致し、変動要因が少なく作成したスケジュール通りに実世界でも実行できる場合には、有効な手法であると言えます。実際、このような条件を満たし、かつ人が作成するのが困難な大規模なスケジューリング問題では、大いに力を発揮しています。しかし、逆に対象とする系に変動要因が多くモデルが複雑になるほど、この手法の適合性は低下するでしょう。
③の方法は、①の方法を除けばスケジューリングシステムとして最もよく利用されている手法であると思われます。この手法によれば、コンピュータを使って実行可能なスケジュールを高速で作成できるので、その結果を見て人が修正を加えたりパラメータを変えて再スケジューリングしたりといった、インタラクティブなスケジューリング作業が可能です。市販の汎用スケジューリングソフトウェアの多くは、このようなアプローチを採っているものと考えられます。この手法の問題点としては、上表に示すように、少なくとも従来のスケジューリングソフトウェアの場合、対象システムのモデル化機能に限界があること、および変動要因のスケジュールに与える影響を定量化できないことが挙げられますが、このような部分を人がカバーすることで、実用的なスケジューリングシステムを実現していると見ることもできます。
Simioの提供するリスクベースド・プランニング&スケジューリング(RPS)の機能は、その基本的な枠組みは③に分類できますが、表に示した二つの問題点を克服している点で、他のスケジューリングシステムとは一線を画するものです。以下に、その詳細について説明します。なお、以下の説明では理解を容易にするため、主に工場における生産システムのスケジューリングを例にとって説明しますが、その基本的な考え方は、あらゆる分野のスケジューリング問題にも適用できるものです。
詳細なモデル化の重要性
工場における生産システムのスケジューリングでは、オーダーに対する主要なリソースの割り当てや在庫制約以外にも、真に実行可能なスケジュールを作成するため、様々な付加的制約条件や付加的経験則を考慮したい場合があります。たとえば、大工程を構成する中工程・小工程に付随する細かな制約条件、それらの工程に関連付けられるスケジューリングの経験則、工程間の中間製品の搬送や仮置きスペースに関する制約など、通常のスケジューリングシステムでは考慮されないことの多い詳細要素が、重要な意味をもつケースです。最近の市販のスケジューリングソフトウェアでは、これらの点についてもかなりの改善が図られているようですが、離散系シミュレーションソフトウェアのような独立したモデリング環境を持たないため、対象システムのモデリングの詳細化には、自ずと限界があります。従って、スケジューリングシステムがカバーできない詳細レベルの要因を考慮したい場合は、人に頼る必要があります。離散系シミュレーションソフトウェアの機能を持つSimioには、このようなモデルの詳細度に関する制約がないため、Simioを使って対象に応じて必要なレベルの詳細度のモデルを作成し、それをベースにスケジュールを作成すれば、真に実行可能なスケジュールを常に作成することが可能となります。
”変動”を考慮することの重要性
スケジューリングシステムは、ある時点で入手可能な与条件に基づいてスケジュールを作成しますが、その与条件は将来”変動”する可能性を含んでいるのが普通です。また、作成されたスケジュールは将来起こりうる設備の故障や作業人員の病欠などのリスクに常にさらされているのも事実です。従って、作成されたスケジュールの実行過程では、様々な”変動”要因のため、現実の進行状況はスケジュールから乖離していくのが普通であり、もはや初期のスケジュールが守れないと判断されたら、再スケジューリングを行うことになります。現状のスケジューリングシステムの問題点のひとつは、このような”変動”要因をスケジュール作成時点で定量的に扱うことができないことにあります。そのため、スケジュール作成者は、過去の経験に基づいて工程間に時間の余裕を設けたり、リソースの余裕を考慮したりすることで、このような”変動”の影響を最小限に留めるよう努力します。一方、離散系シミュレーションソフトウェアの機能を持つSimioの場合、与条件の”変動”を確率分布として与え、複数回のシミュレーションを反復実行することで、それらの”変動”が実行結果に与える影響を同じく確率分布として定量化できます。
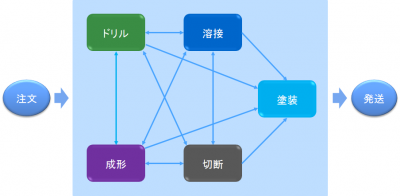
図ー1.生産システムの例
たとえば、図-1.に示すような注文生産を行う生産システムがあり、オーダーの種類にによって工程順序と工程期間が異なるものとします。またスケジュール作成時点での工程期間の見積りや設備稼働率には、かなりの不確実性を伴うものとします。この生産システムに対して5つのオーダーをスケジューリングする場合、各オーダーに対する納期回答は、”変動”を考慮しない従来のスケジューリングシステムでは図-2.に示すように全てのオーダーについてOn timeとなっていますが、”変動”を定量的に評価したリスクベースド・プランニング&スケジューリング(RPS)によるスケジューリングでは、図-3.に示すように2番目と5番目のオーダーについて納期遅れのリスクが高いことが示されています。この例のように、Simioの提供するRPSの機能は、スケジュール作成時の与条件の”変動”の可能性が実行結果に与えるインパクトを定量的に評価できるため、スケジュールの内包するリスクを定量的に管理することが可能となり、またより”変動”に強いスケジュールの作成も期待できます。
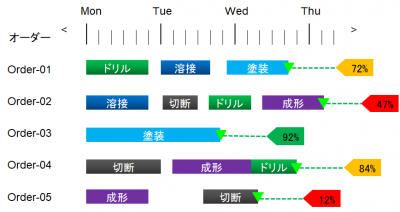
図ー3.RPSによるスケジューリング
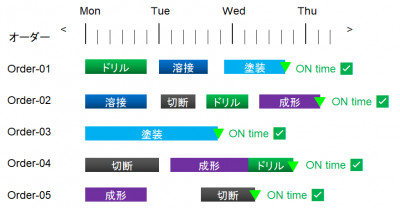
図ー2.従来のスケジューリング
RPSの適用範囲
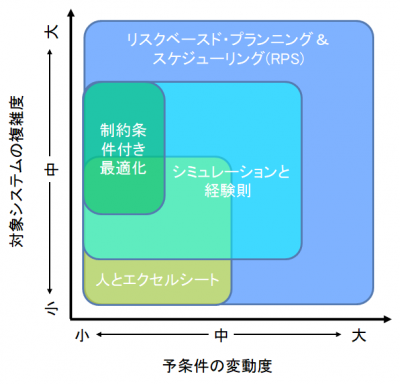
図ー4.RPSの適用範囲
以上に示したように、Simioの離散系シミュレーションの機能を基礎とするリスクベースド・プランニング&スケジューリング(RPS)の機能は、シミュレーションと経験則に基づく通常のスケジューリングシステムの利点を踏襲しながら、対象とするシステムのモデル化の詳細度に制約がないことおよび与条件の”変動”を定量的に扱うことができることから、スケジューリングシステムに新しいパラダイムを提供します。図-4.に示すように、Simioの提供するRPSの機能は、従来のスケジューリングシステでは扱うことが困難であった広い領域をカバーできる優れた汎用性と機能性を提供します。
それでは、Simioを使ったスケジューリングシステムとはどのようなものでしょうか?Simioは、スケジューリングシステムの実装段階で役立つ機能も豊富に備えており、このことは、Simioを使った場合のスケジューリングシステム開発の迅速化と品質の向上に貢献します。以下では、スケジューリングシステムの特徴とSimioによる実装の利点についてご紹介します。
Simioによるスケジューリングシステム構築
一般に、スケジューリングシステムはその機能を果たすために以下の4種類の入力情報を必要とします。
- 生産計画情報
- 設備能力・製品定義情報
- 資材情報
- 生産進捗情報
生産計画情報は、注文情報そのものであったり、見込み生産計画であったりしますが、いずれにしてもスケジュール作成の対象となる生産要求の情報です。設備能力・製品定義情報は、製品製造の個々の工程で使用可能な設備の情報(台数、処理能力、搬送能力、在庫容量など)、作業に従事できる人員や能力・資格に関する情報、および製品毎の製造工程や資材要求量などで、通常はマスタとして管理されるべき情報です。シミュレーションモデルを使うスケジューリングシステムの場合は、モデルの定義情報と言いかえることができます。資材情報は、生産要求を実行する上で必要となる資材(原料、部品、その他の副資材)の在庫情報や入庫予定の情報です。最後の生産進捗情報は、スケジュール作成の基点となる時刻(通常はスケジュール作成時点より少し先の時刻)の生産進捗を推定するために必要となる、最新の生産進捗状況に関する情報です。これらの情報に基づいて作成された生産スケジュールは、通常は製造実行システム(MES)に送られ、MESからの指示に基づいて実際の製造作業が実施されます。生産スケジュールは通常1日、1週間、1ヶ月といった定周期で更新され、その都度スケジュールと実際の生産進捗のギャップが生産進捗情報に基づいて調整されることになります。
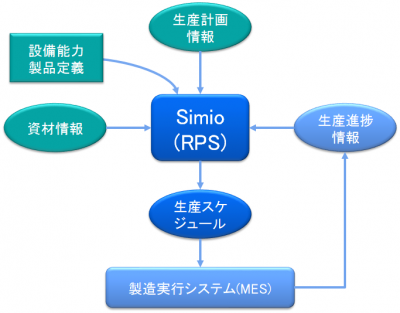
図ー5.RPSと入出力情報
これらの情報の流れを図ー5.に模式的に示します。実際のスケジューリングシステムの設計に当たっては、これらの情報をどのようにスケジューリングシステムに取り込むかを、検討する必要があります。もし、これらの情報を全て自動で電子的に他のシステムから入手可能であれば理想的ですが、通常は情報の一部を手動で入力することになる場合が多いと思われます。
Simioは、データの手動入力はもちろんのこと、エクセルファイルやCSVファイルからの読み込み、外部データベースからの読み込み、およびXMLデータの読み込みが可能で、外部システムとの緊密な連係が可能です。またSimioの内部にリレーショナルデータベース構造のデータを保持できるので、本社の基幹システム(ERP)や工場の製造実行システム(MES)に必要な情報が集積されている場合には、これらのシステムのデータをそのデータ構造を変えることなく一括して読み込むことも可能です。このようにすることで、外部システムとのデータ連携に伴うインタフェース設計の作業を軽減することができ、システム構築作業の大幅な効率化が可能となります。また、ISA-95に準拠したデータ構造(B2MML準拠のデータ構造)を持つMESやWoderware社の MESの場合は、Simio側でこれらに準拠したデータ構造を自動的に生成することができるので、さらに効率的なシステムインテグレーションが可能となります。
Simioがスケジューリングにおいて使用する離散系シミュレーションモデルは、Simioの提供する通常のモデル作成インタフェースを使って作成する(Model Driven Approach)ことはもちろん可能ですが、設備能力や製品定義に関する情報がERPやMESなどの外部システムから入手可能な場合は、その情報を使ってモデルを作成する(Data Driven Approach)ことも可能となっています。特に大規模かつ複雑な施設の場合で、他の目的で離散系シミュレーションモデルを作成していないケースでは、後者の方法はモデル作成の手間を大幅に削減します。
Simioの現場への導入段階では、実データによる検証作業が欠かせません。常に実行可能なスケジュールが作成できているか、既存のスケジューリングシステムの作成するスケジュールと比較してより良いスケジュールが作成できているか、といった観点でチェックを行い、考慮されていない制約条件があればそれらをモデルに追加し、スケジュール生成に適用される経験則に問題があるようであれば、その経験則をより適切なものに置き換えるなどの対策を行います。ここでのSimioの利点は、シミュレーションモデルとスケジュール作成の規則が共に明示的であるため、これらの変更の理由・内容および結果を関係者の誰もが容易に理解できるところにあります。このようなステップを通じて、Simioを使ったスケジューリングシステムは、将来に渡って安心して使用できるシステムとして関係者に受け入れられるものと考えられます。
Simioを使用したスケジューリングシステムの構成例を図ー6.に示します。スケジューリングシステムの必要とする情報を全てMESから入手できるのが理想ですが、通常はERPやその他のシステムからも情報を受け取る必要がある場合が多いと考えられます。もし、手動で入力する情報をなくすことができるのであれば、スケジュール作成の半自動化や全自動化までも視野に入れることができるでしょう。いずれにしても、Simioの高速かつ信頼性の高いスケジュール作成機能は、スケジュール作成担当者の負荷を大幅に軽減することは間違いありません。
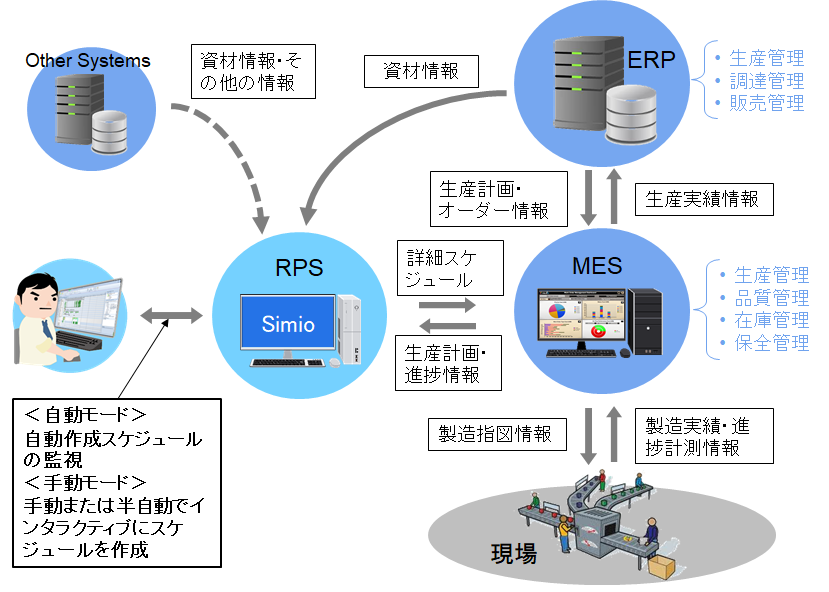
図ー6.RPSシステムの構成例
SimioとIndustry4.0
以上で見て来たように、Simioのリスクベースド・プランニング&スケジューリング(RPS)の機能は、生産システムのスケジューリングに従来にない以下のメリットをもたらします。
- 離散系シミュレーションの柔軟なモデリング機能は生産現場のあらゆる制約のモデル化を可能とし、常に実行可能なスケジュールの生成を保証する
- スケジュール作成の前提条件の変動の、納期などへの影響を定量化することが可能であり、その結果、より信頼性の高いスケジュールの作成が可能となる
- リレーショナルデータベース構造のデータを保持できるため、外部のシステムとのインテグレーションが容易となる
- データからモデルを作成する手段(Data Driven Approach)が提供されているので、大規模なシステムの構築にも容易に対応できる
- 入力情報を外部システムから全て自動的に入手可能であれば、半自動または全自動のスケジューリングシステムの実現も視野に入れることができる
- ユーザーにとって、シミュレーションモデルとスケジュール作成規則の可読性が高いので、ユーザーによる保守が容易となる
- 離散系シミュレーションのアニメーション機能はを使えば、スケジュール作成のステップを可視化することも可能で、これによって関係者の理解を深めることができる
最近の先進的な製造工場では、ERPやMESの導入とネットワークインフラの構築、および個別機器の自動化は概ね達成されています。しかしながら、個別機器の間の協調的な制御やインテリジェントなスケジューリングはまだ十分とは言えないことが多いようです。高度に自動化されたスマートファクトリー、あるいはIndusry4.0の実現が、今日の製造業の主目標であるとすれば、Simioは、その実現をシミュレーション機能による将来予測、アニメーションによる可視化、そしてスケジューリング機能による意思決定を通じて強力にサポートするツールであると言えるでしょう。
Simioには、製造業だけに留まらず、様々な産業分野での注目される導入事例があります。最近の導入事例のいくつかを、次のページでご紹介します。